InnoBMS project
About InnoBMS
Todays´ battery management systems (BMSs) are based on static algorithms and functions that receive fixed input parameters calibrated from predefined and generalized (driving) conditions. Creating a situationally aware BMS with a dynamic response will help to overcome the existing barriers and to use batteries and valuable resources more efficiently. Situational awareness for a BMS means that it (1) receives battery-related information that is representative of the actual conditions and (2) can interpret that information to understand the situation it needs to operate in. Actual-state battery information and the ability to process that input enables the BMS to take balanced decisions for optimal use and maximum battery life in every situation.
Objectives
Models and algorithms to enable a flexible BMS that is suitable for a range of batteries, and that is fully informed to take balanced decisions for safe and optimal battery use in every driving condition.
Software for a wireless BMS with reliable and secure connections between all actors in the battery system.
A scalable, fully wireless, self-testing BMS hardware that enables OEMs to use different battery sizes (energy content) at different operating voltage levels (e.g., 400 and 1000V), and sensor integration.
Better use and exploitation of the battery using on cloud-informed strategies and procedures, including full diagnostics for data-informed non-primary use (predictive maintenance, 2nd life, V2X capabilities).
Technical Multiple demonstrations of these innovations integrated in a vehicle by using new simulation tools and automated test methods to develop a more efficient BMS in a shorter time (virtual & physical use cases).
Communication, dissemination and exploitation of the InnoBMS results.
Concept
The core objective of InnoBMS is to develop and demonstrate the best-in-class BMS hard- and software solution that maximizes battery performance for the user without negatively affecting battery life, even in extreme conditions, whilst maintaining durability and safety at all times.
Approach
The InnoBMS project starts with defining all requirements and specifications (indicated in yellow). The technical work itself is divided into three development levels. The research level is indicated in green. At this level, the advanced modelling in the cloud is developed. The integration level is indicated in blue. At this level, the embedded software for the on-board BMS is written, the models are integrated into the operational software and all physical components are integrated into the on-board BMS hardware. It is at this level that the final BMS product is built (grey box). Finally, the demonstration level is indicated in orange. At this level, the final BMS product is demonstrated in virtual and real vehicle tests, and the automated test methods are developed to enable this. The figure also mentions the work packages. WP1 is Requirements, design specifications and use-case demos; WP2 is advanced functionalities, simulation and testing methods; WP3 is BMS Software & connected functionalities integration, WP4 is advanced BMS hardware and integration with advanced sensors; WP5 is Testing, validation and demonstration.
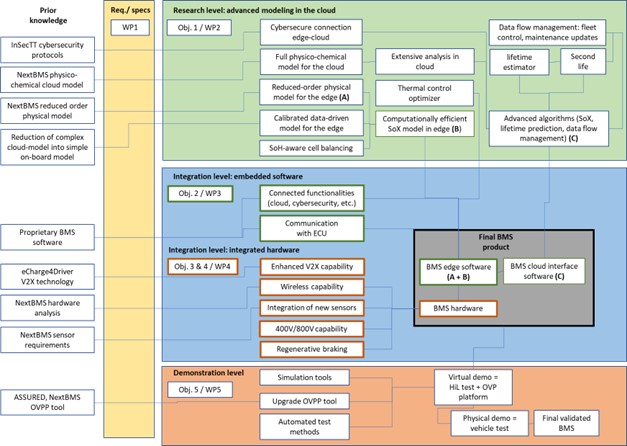
Structure
The InnoBMS workplan is divided into:
- 5 research-related work packages
- 1 dissemination work package
- 1 management related work package
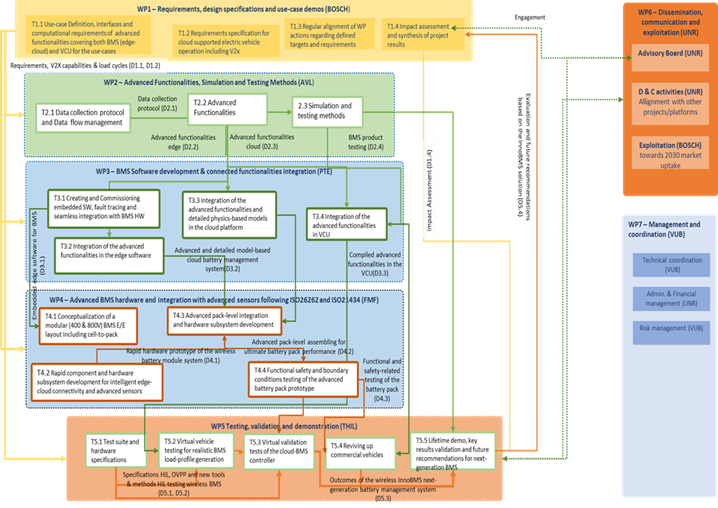
Results
The InnoBMS Consortium expects the following project outcomes:
- An integrated system, highly connected and self-testing, for balanced decisions, using input from from sensors, VCU and cloud, based on accurate predictive models
- Predictive SoX diagnostics to accurately determine the actual state of the battery for optimal power, fast charging, regenerative breaking, maintenance and end-of-life predictions
- Use of advanced models (physics-based and data-driven) and secure real-time battery management to reduce margins, based on cell-level data, with simplified algorithms running in the vehicle, supported by a digital twin running in the cloud
- Collecting and managing data for accurate second life classification, and interfacing to Vehicle-to-everything (V2X) applications
- A BMS validated at TRL6 in real driving conditions, in a real vehicle, that enables a battery lifetime of 15 years
These outcomes will be represented in the use cases depicted in the figure below.
Facts and figures
Acronym: InnoBMS
Duration: 42 months
Start date: 01-01-2024
Total budget: €5,672,894.38
EC Funding: €4,013,441.88
Publications
InnoBMS will disseminate scientific results to peers in the field of batteries and BMS by means of scientific publications. All relevant publications will be posted on this page.